This information has been provided by AMC Filter® to explain how they achieve high quality standards, they also take you through the production process of the oil filters, fuel filters, air filters & cabin air filters.
The AMC brand is for many years a well respected brand for the OE and Aftermarket. The AMC filters are supplied to OE suppliers like Toyota, Hitachi, SsangYong, Nissan and Suzuki.
The filters are produced according to the JAPA standard in modern factories with all necessary facilities to produce high quality filters.
Japan Automotive Products Association (JAPA) is an association which tries to improve the quality and performance of the auto parts. The association has been set up the following standard for the recommendable products, as aiming to customer's easy selection of safe and reliable products:
- The filters are approved with indication of JIS (Japan Industrial Standard) mark and passed the safety standard.
- The filters are produced by Original Equipment Manufactures (OEM) to car makers.
- The products are such good quality as guaranteed by the Public Testing Organization, by the factory diagnosis organization or by recommendation system of manufacturers and/or other official system. (for example ISO)
Used materials
The most essential part of the filter is the quality of the filter media (mostly paper). The function of the paper is to separate the damaging parts like dust and metal particles etc. from the oil. The clean oil will flow back in the engine and ensures a good performance of the engine.
The variety of filters is enormous. This because filtration specification for different engines are not the same and therefore the filters are not the same.
Before a particular paper is used in a filter it passes a few test stages:
- The paper is being checked on quality in relation to the OE filter were for example micron rating, air permeability and particle counter are being analyzed.
- After the filter medium is examined the engineers define the quality standard for the medium and start testing the chosen paper to check if it reaches the requirements.
- In case the results does meet the high standards of the AMC guidelines the bodywork and other inside details will be developed further. If the requirements are not being met, a new medium will be developed together with the manufacturer of the medium which will lead to a satisfied result.
Not only the paper material but also the other materials like the metal parts and the rubber seal are chosen very carefully and tested before AMC will finally use the products.
Testing
After the total design is ready a few samples are being produced for further detailed testing. Depending on the filter type it has to pass one or more of the following tests: impulse test, salt spray test, vibration test, burst test, thermal cycle test and/or pull- and push test.
The inspections of the filters are carried out by quality control personnel, which are all trained and certified, also all the inspections are done by adequate and calibrated measuring devices.
All the production processes are being controlled (without any exception) according the high Japanese standards. During every new set up of each process as well as periodical the line/station personnel (line station manager) is checking the result. As a double check the general quality control manager looks after the correctness of the quality check done by the line station manager. Critical parameters, concerning the oil and fuel filters, checked by a leak test is being done 100% (every single filter) with no exceptions.
Vision of AMC
AMC is a high quality product which is produced under strict procedures and the best possible circumstances before it is being mounted under the bonnet of the end-users car. The end-user is ensured of a high quality filter which guarantees a good performance of the engine for many kilometers. AMC is proud on their high quality products and a good name in the market.
Japanese Automotive Products Association (JAPA)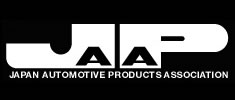
JAPA is a association consisting of trading companies which sell automotive spare parts to all over Japan and the world (official members) and automotive parts manufacturers (sub members).
“Superior Parts” Certificate of superior parts given by JAPA
The maintenance parts supplied with its own brand and distribution of the car manufacturers are called “genuine parts”, while exchange parts for maintenance which are guaranteed the same or better quality than “genuine parts” by car manufacturers are called “superior parts”. These superior parts are supplied to users all over the world through JAPA members. JAPA started “recommendation for superior parts” in 1972 in order for users to use “superior parts” with contentment. The purpose of this certificate is to contribute a profit for users as well as boost the reliance on the products of the car industry through supplying and spreading “superior parts” all over the world.
The credence has some standards for users to choose the brand without hesistance.
- Products permitted by JIS and given the security mark
- Products guaranteed its high quality by scrutinizes of both public and private testing agencies.
- Products are supplied to assemble a car through car manufacturers.
The association recommends the products of “superior parts” under the three standards above, and will make the best effort for the contribution to consumer’s benefit.
AMC OIL FILTERS
Where the oil is the substance, which lubricates and cools working parts, it also rinses out and transports all kinds of contaminants in the form of suspended matter from the combustion chamber, forming during the abrasive wear of working parts of the engine.
Such contaminants are effectively trapped in filters, which are an important element of the lubricating system in any engine.
However it should be noted that these filters cannot stop the oil degradation which is an irreversible chemical process and that is why, regardless of the kind of filter installed in ones car, the oil should be changed in accordance with the car manufacturer indications (including filters).
The oil filters have different shapes and depending on the engine type may differ significantly regarding construction and principle of operation.
Full Flow Spin-On Type
Can type oil filters are used mainly for filtering oil in engines. However, in modern engines these filters are less popular. Previously important advantages such as good resistance to damage and easy replacement of used filters, practically with no risk of oil system contamination are not the priority anymore.
Presently the ecological aspects, especially easy filters utilization are more important. In this respect, modern filter cartridges installed in dismountable casings are better.
The appearance of can type oil filters are very similar, but the internal construction features for this group of filters must be optimally selected, to assure efficient operation in the engine oil system.
Bypass Spin-On Type
The high capacity engines often have oil systems with two types of filters. One full flow - all the oil pumped flows through, while the second is built into the system in parallel and about 10% of oil flows through it.
This oil, after being purified, goes back into the oil tank. The full-flow functions as a coarse filter, while the by-pass filter is the fine filter in this system.
In the oil system, centrifugal filters are often applied as by-pass filters, where contaminants are separated from the oil in the centrifugal field of force. Filter are also used, made with a medium of special fabrics or filtering papers.
The characteristic feature of by-pass filters with the medium is the amount of oil reduction during exploitation, which results from flow resistance increasing during the filter medium blocking.
In some engines with full flow/by-pass oil system, the can filters with two filtering cartridges (full-flow & by-pass) are applied.
Such integrated filter systems take less space and its re-placement is much quicker. The oil flow in such filters is divided into the main flow directed into the engine and by-pass flow, which after proper purifications flows back into the oil tank.
Combination Type
Specially, the high capacity diesel engine use the combination type oil filter the oil from the oil pump is not split. All the oil from the pump is sent to a filter, where it passes through the full flow element and then by-pass elements provided.
After filtration, the oil flows in the same way as the full-flow type employs a special structure that provides internal oil pressure difference to allow both the full flow and by-pass elements to maintain their specified filtering ratio.
The by-pass element used, is made with a medium of special fabrics or filter papers.
Importance Of The Anti-Drain Valve
Generally, the anti-drain back valve have the form of a rubber membrane adjoining the inner side of the can type filter cover. The membrane covers the holes where the contaminated oil gets through the filter and protects from the back flow after the engine stops. The anti-drain back valve reduces the dry friction or mitigated solid friction time between working parts of the engine as protecting from the oil flow towards the pump and accelerates the oil flow into the working elements during the engine start, especially after a long break. The position of the filter is screwed into the engine, conditions the valve application. If the filter works in the "cover up" position the function of the valve is taken successfully by the gravitation. A valve is required when the filter in sore-wed in from the side or from the top of the engine body.
Importance Of The By-Pass Valve
The by-pass valve is always installed in the oil system with full-flow filter (installed in series in the system). Usually it is built in the filter itself; however there are constructions where this valve is placed in the engine body. Regardless of the place where it is installed, its only function is to clear the oil flow when the flow resistance is too high and there is a risk of insufficient lubrication of working parts. It is considered though that lubricating and cooling with contaminated oil is less damaging than the lack of lubrication which may lead even to the engine seizing. There are basically two reasons why the oil flow resistance in the filter, opens the by-pass valve. First: high density which happens in winter at low temperature.
While starting the car after a long stop (i.e. going to work in the morning), the cold and thick oil flows on the filter medium which makes the flow difficult. The pressure increase makes the by-pass valve open. The second reason for the by-pass valve opening is the filter medium wear. When the filter is excessively contaminated, its filter medium is chocked by contaminants. In this case it may happen that the by-pass valve is continuously open. To avoid such situations, it is required to change filters and oil in accordance with the car manufacturer's recommendations.
Oil Filter Performance Test
Test Carried Out | Requirements & Results |
Initial bubble rate (%) | Not less than 50% |
Pressure drop (kgf/§2) (or mpa) | Not greater than 0.3 (not greater than 0.02942) |
By-pass valve opening pressure | Within a range of opening pressure specified |
Filter efficiency (%) | Not less than 80% at 11th hours, and not less than 90% at the end of the test |
Contaminant capacity ratio | Class 1st: Not less than 0.25. Class 2: Not less than 0.30 |
Drain back Oil | Not greater than 100 |
Resistance to differential pressure of filter element | Filter element shall withstand a pressure differential of 5 kgf/§2 (or 0.4903 Mpa0 with evidence of failure |
Proof pressure | Filter shall withstand a proof pressure of 15 kgf/§2 (or 1.471 Mpa) Without evidence of external leakage of harmful defect |
Impulse | Filter shall withstand 4x10 impulse cycles without evidence of external leakage |
Vibration | Filter shall withstand 5x10 vibrations without evidence of external leakage |
AMC AIR FILTERS
Air filter trap solid particles such as mineral dust, soot, and organic pieces floating in the air, which is sucked in by the engine. The progress in filter constructing and application of modern filtration materials brings the level of contaminants filtration to the level of 99.9% for particles of even few micrometres size. Whereas the engines use a great amount of air during combustion process (average amount of 10 m3 of air per 1 litre of fuel), filters with high filtering efficiency must also have low flow resistance and high contaminants absorptivity. Due to such properties, it is possible to extend the period between filter replacements. Modern air filters used in the automotive industry are designed and constructed in versatile shapes and sizes and made of different, optimally selected materials.
Performance Test Air Filter
Test | Requirements |
Air Flow Resistance | Should be within prescribed value |
Pressure drop (kgf/§2) (or Mpa) | Gasoline engine over 97.5%
Diesel engine over 98.5% |
Life cleaning efficiency | Gasoline engine over 98%
Diesel engine over 99% |
Recovery attribute | Over 97% |
Destructiveness & Punching test | Should be no destruction or punching in |
AMC FUEL FILTERS
Fuel filter trap contaminants in fuel, oil, diesel oil in LPG installations, providing efficient protection to precise elements of the engines fuel systems from quick wear. These fuels contain contaminants resulting from the production process and distribution. Dust, soot from outer tank surfaces, water and microorganism may cause quick wear of injectors, pumps, or pressure regulating valves in modern engines. Therefore each fuel system has a filter which is optimally selected according to engine requirements, fuel quality and expected exploitation conditions. Requirements for filters are very high. The filtering for modern engines is required for contaminants particles size 3/5 um with over 90% efficiency. For better performance, more than one filter is installed in the fuel system in many cases. However in comparison with oil filtration, there are no by-pass valves in fuel filtration which clear the fuel flow, when the filters are clogged, as it is rule that only clean fuel goes into the combustion chamber. Therefore it is better that the engine stops due to lack of fuel (dirty filters) than if it had to work using non filtered fuel.
Can Type Filter
Can type filters are usually applied as fine filters and coarse filters in multistage filtration systems, and there are often filters used with characteristic drain plugs inside the separator. Water generally does not dissolve in fuel, but remains as drops or emulsion causing corrosion process intensification of metal parts in fuel system. Water is removed from fuel using sedimentation effect (gravitation drops settling in decanters) and coalescence – water drops separation in fuel flow through filter medium. These filters are designed similarly as can type oil filters, however, they do not have any inner valves. The filter replacement process is also similar and means only unscrewing the used filter and tightening the new one. Also as in the case of spin-on oil filters, used filters disposal is expensive and this model is widely replaced by ECO cartridges.
Injection Filter
Injection filters are applied in fuel systems, especially in petrol carburettor engines and fuel injection engines, installed on the fuel pipe using quick connect fittings or band clips. These filters have a filtering cartridge with paper medium, which is pleated or warped. Warped cartridges are made of special, thin filtering material. It has a highly filtration efficiency but limited absorbability; hence the filtering medium surface for these filters must be larger than for filters with pleated medium.
AMC CABIN AIR FILTERS
Cabin air filters are used for filtering air which is sucked in directly from the road, forced in through ventilation or air conditioning system into the driver's cab. Most of the modern manufactured cars are equipped with these filters, as it is no more a synonym of luxury but the safety requirement.
Tiredness, allergic rhinitis, eye watering or breathing disorder have definitely a negative impact on the driver's reflexes and might be really dangerous for road safety. These symptoms are often caused by contaminants coming into the driver's cab with the air sucked in. The concentration of certain types of contaminants results from a number of factors such as season, weather conditions, noxiousness of local industry and road traffic intensity. Air dustiness may reach a level six times higher than outside the car in vehicles not equipped with dust filters, as with the working ventilator, the cabin acts as a decanter.
Breathing contaminated air causes negative, often an irreversible impact on the human's health. Despite natural barriers and defence mechanism, which means the ability for self-cleaning of respiratory tracks and lungs, most of the solid banks gets into the bronchial tubes or even into the pulmonary alveolus, becoming often the source of infections. Cabin filter efficiency can be easily noticed during replacement. The surface of used filter shows exactly what it is about. Being aware that all what settles on filters might have been in our lungs should probably be the best argument for using filters in our car.
Standard Cabin Air Filter
Dust filters have a filtering medium made entirely from synthetic fabric. Excellent efficiency in filtering particles of sizes smaller than 1§ results from the effect of contaminants attraction by electro statically loaded fibres. Due to this effect, contaminants of sizes smaller than pores in the filtering medium maybe efficiently trapped. Smaller particles simply get stuck to fibres. Once they come close, the electrostatic attractive force is stronger than the force of particles flow caused by the air blast. Synthetic fibres are slightly hygroscopic, so dust filters do not get deformed from water. They also have antiseptic properties (they are not favourable to microorganisms), and therefore are efficient in stopping microorganisms development and organic contaminants decomposition in the filter during exploitation period.
Cabin Filters With Active Carbon
Dust filters with active carbon are a special group of filters. The filtration medium consists of two outer layers made of synthetics fabric, capable of trapping solid particles and aerosols with efficiency equal to standard dust filters. Additional, third layer of filtering medium placed inside fabric layers is an active carbon granulate, which filters the air from harmful gases. The active carbon has a porous structure similar to graphite. It attracts harmful gases to its surface due to the effect of absorption. The specific surface of one gram of active carbon comes to even 900 §³ and therefore the amount of gases stopped may be significant. Practically, the amount of active carbon in filters allows eliminating about 90% of harmful gases such as ozone, hydrocarbons and nitrogen compounds during the whole filter exploitation period.
> Click here to view our AMC Oil, Air and Fuel Filters; as well as our Filter Kits.